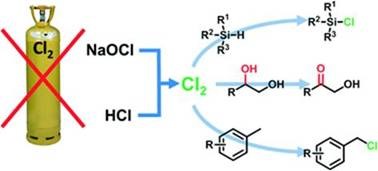
Date: 30 August 2016 | Category: News
In an excellent paper from the group of Oliver Kappe, University of Graz and RCPE, a Vapourtec E-Series and UV-150 photochemical continuous flow reactor has been at the forefront of the development of in-situ chlorine generation for a much safer method of working with this powerfully oxidising and reactive gas.
Chlorination of organic compounds for use as reagents is a very important synthetic strategy, but even though the use of elemental chlorine results in a vast array of synthetically useful compounds, it is typically a considerable undertaking. The toxicity of chlorine gas is infamous and users have to be specially trained and equipped to handle it safely. As a result, chlorination by elemental chlorine is not accessible to many typical research groups or even many industrial facilities. Even once the hazards of chlorine are managed, its high reactivity often results in significant exotherms that can be difficult to control, and can result in poor selectivity due to overreaction and side reactions. The large surface area to volume ratio offered by the Vapourtec E-Series provides excellent thermal contact with the reactor, allowing exotherms to be dissipated quickly, making continuous flow an ideal medium for carrying out reactions with elemental chlorine
Kappe’s group have demonstrated how readily accessible, easy to handle and inexpensive HCl and NaOCl can be used to liberate elemental chlorine in situ by pumping the two feedstocks in water, using the V-3 pumps of a Vapourtec E-Series, and mixing the streams in a static mixer. It is observed that gas is evolved very rapidly as the streams mix, but the operator is protected from the hazards of the chlorine by generating the small quantities inside the reactor. Mixing with an organic solvent creates a biphasic mixture, with the chlorine dissolved in the new organic stream. A commercial liquid-liquid membrane separator, from Zaiput and fully compatible with the Vapourtec system, is then used to remove the water, leaving an organic phase that is dense with elemental chlorine. To demonstrate the technique, Kappe’s group chlorinated Triisopropyl-, dimethylphenyl- and triphenylsilane to the equivalent chlorosilanes, with significant success. Full, selective conversion to the chlorosilanes was observed and solvent evaporation gave quantitative amounts of the pure products. Success was also achieved using a chloro-pyridine complex to selectively oxidise secondary alcohols. This was demonstrated by in-situ formation of the oxidising species followed by selective oxidation of 1,2-hexanediol to 1-hydroxy-2hexanone, with a conversion and selectivity of 99% respectively, in just 15 minutes.
In a final demonstration, Kappe’s group undertook the photochlorination of a series of substituted toluenes, using the Vapourtec UV-150 continuous flow photochemical reactor equipped with a Hg lamp, and filtered to a cut-off of 300 nm. Toluene was used as a model system for finding the optimal reaction conditions, which transferred well to various toluene derivatives, carrying both electron donating and withdrawing groups. In the paper, Kappe observes “the high efficiency of this continuous flow photochemical chlorination (80 – 99% yield in 10 – 15 mins) is in contrast with the poor results typically obtained in batch where several hours of irradiation under reflux are typically required”.
“The benefit of using flow chemistry for the safer handling of hazardous materials is well documented” comments Dr Ryan Skilton, Vapourtec’s Research Scientist “and here the Kappe group have demonstrated that to great effect. The easy to operate E-Series gives very quick access to those benefits, and the compatibility with other commercial technology like the Zaiput membrane separator give the system great versatility. The UV-150 has also been used very successfully, and the range of available filters allowed the Kappe group to output the most efficient wavelength for their intended reaction, potentially reducing the activation of unwanted transformations”.
To read more about the UV-150 click here
To go directly to the Reaction Chemistry & Engineering click here