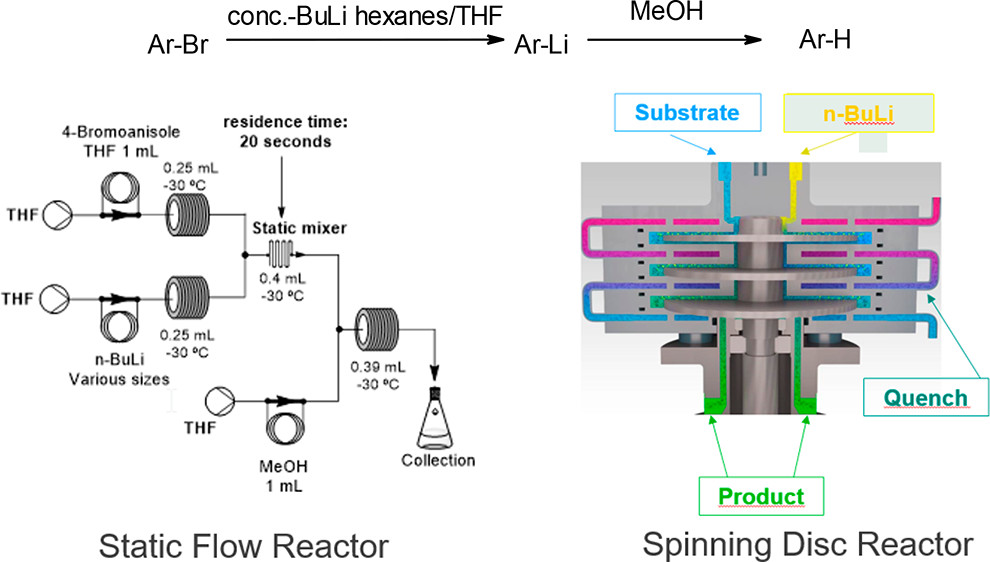
Date: 29 June 2022 | Category: News
Wietelmann et al., Org. Process. Res. Dev. 2022
Organometallic chemistry is a tool widely used in organic synthesis. However, due to their high reactivity and potential pyrophoricity in air, organolithium compounds are considered dangerous and often require expensive cryogenic process conditions. This creates challenges when using such reagents on an industrial scale. Moving from classical batch processes to flow reaction setups can provide key advantages for process safety and economics.
In this study, Wietelmann et al. compare static and dynamic flow reactor technologies for two important organolithium-enabled transformations: deprotonations and bromine/lithium exchange reactions. In continuous flow, reactor fouling can be a serious challenge. Hydrocarbon solvents present in diluted (1.6 – 2.5 M) standard commercial butyllithium (BuLi) solutions act as antisolvents, leading to the formation of solids, which can block flow reactors. Decreasing the hydrocarbon content by using concentrated (≥3 M) organolithium solutions and replacing them with donor solvents such as tetrahydrofuran (THF) helps to overcome this obstacle. By reducing the precipitation of side products, the yield and the robustness of Br/Li exchange and deprotonation reactions can be significantly improved.
Continuous flow allows for cost-effective syntheses of organic products by decreasing processing time, reducing energy consumption, and by using less solvent compared to corresponding batch experiments. In a deprotonation/borylation benchmark experiment,
The team at Albemarle used a Vapourtec R-Series platform for continuous flow lab scale. At just ambient temperature, the yield of a deprotonation/borylation was increased to 78% compared, to just 51% for the semibatch mode procedure carried out at −78 °C.
Performing organolithium processes in continuous flow mode has numerous clear advantages for the manufacture of pharmaceutical intermediates, agrochemicals, and specialty chemicals.
To read the publication featured in this article click here
To find out more about the R-Series flow chemistry system click here