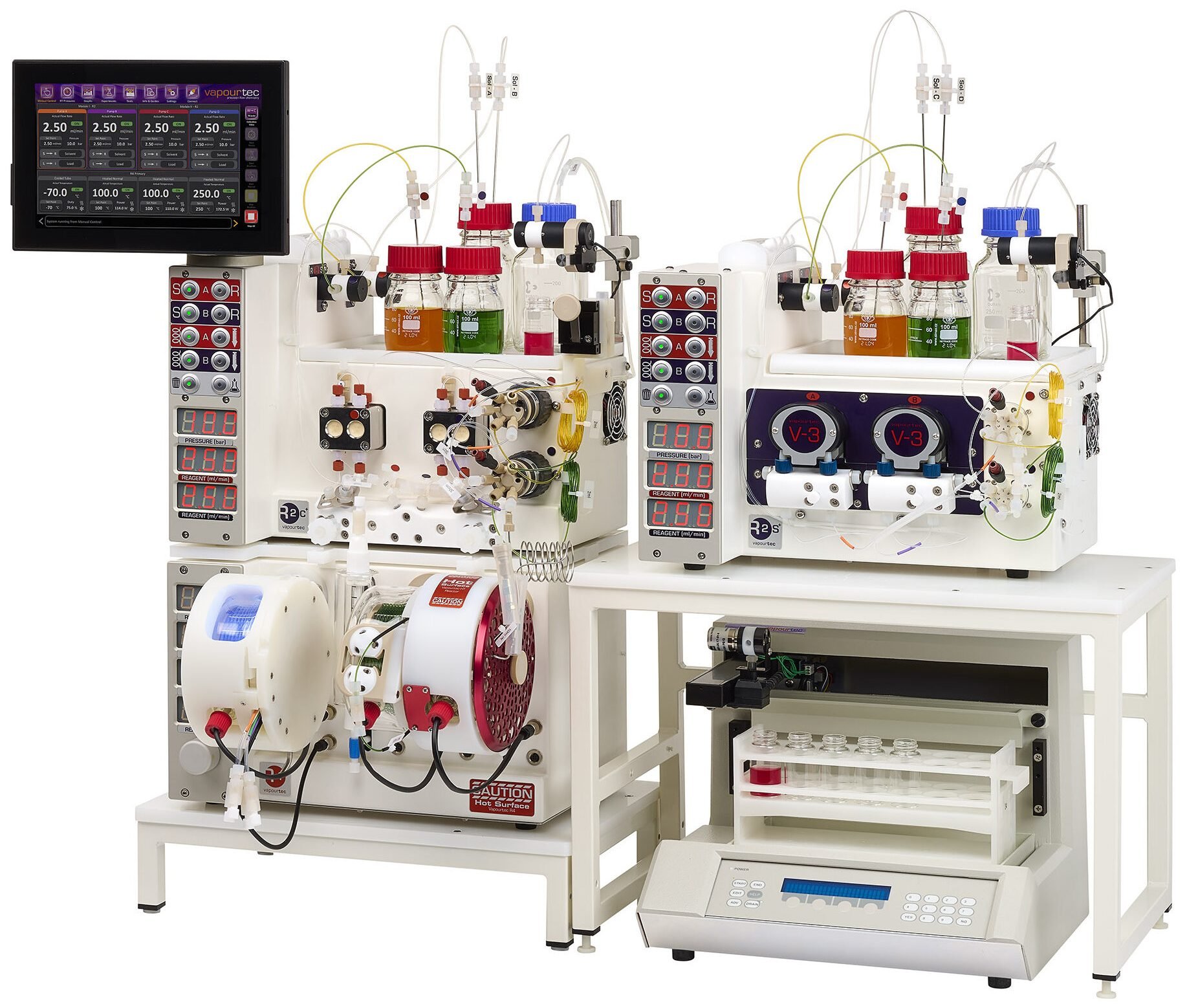
Date: 25 April 2024 | Category: News
Scale-Up of Diazonium Salts and Azides in a Three-Step Continuous Flow Sequence
Hansjoerg Lehmann,* Thomas Ruppen, and Thomas Knoepfel
Researchers in the Global Discovery Chemistry group at Novartis have successfully used the Vapourtec R-Series system to safely scale-up preparation of a key 2H-indazole, 5b, in a telescoped process requiring diazotization, azide formation and cyclisation, all of which are known to be hazardous if performed on larger scale, Figure 1, [1].
Figure 1: Key intermediates in synthesis of TRL7 and TRL8 antagonist, 12.
The discovery of the key compounds was undertaken by medicinal chemists, with the original route completed on small-scale in batch mode. However, as the project was moving towards preclinical studies, the larger quantities required meant that the use of batch mode was no longer a viable approach due to safety considerations.
Flow chemistry has been shown to be a useful tool in the large-scale manufacturing of APIs [2], offering opportunities to improve the safety profile of transformations through the generation and use of species in situ that might be hazardous if isolated [3].
In this case, the key advantages of using flow chemistry were:
- Avoiding isolation of the highly reactive diazonium and azide species;
- Allowing careful control of the reaction temperature, minimizing the risk of thermal runaway;
- Controlling the reaction to minimize formation of undesired by-products;
- The possibility of synthesising large quantities of material rapidly by using continuous processing and telescoping of reaction steps.
The Vapourtec R-Series system was chosen for use due to its facile operation and modularity.
Before commencing, the Novartis team needed to ensure that the reactions themselves were suitable to flow chemistry, therefore any formation of sediment or precipitate needed to be minimised; in this case, the diazonium salt formed as a suspension in batch mode. It was known that solvent and counter-ion can significantly impact the solubility of diazonium salts, therefore a solvent screen was undertaken. Dichloroethane (DCE) in combination with TFA for both the diazotisation and azide formation steps was determined to be suitable, and simple separation followed by removal of some solvent was all that was required before cyclisation.
The careful control of temperature was also key to this reaction sequence, with higher temperature leading to significant safety risk, instability of intermediates and increased by-product formation. The Vapourtec RS-300 equipped with two cooled reactors facilitated rapid preparation of the azide in excellent yield. Over both steps, the minimization of by-products led to higher overall product purity using flow when compared to batch, allowing column chromatography of a late-stage compound to be replaced by simple crystallization.
Finally, the chemical development team were able to adapt the 100 g scale to kilogram scale, using only minor adaptations to the flow procedure disclosed.
References
[1] Scale-Up of Diazonium Salts and Azides in a Three-Step Continuous Flow Sequence (H. Lehmann, T. Ruppen, and T. Knoepfel, Org. Process. Res. Dev., 2022, 26 (4), 1308-1317).
https://pubs.acs.org/doi/10.1021/acs.oprd.2c00016
[2] Continuous-Flow Technology—A Tool for the Safe Manufacturing of Active Pharmaceutical Ingredients (B. Gutmann, D. Cantillo, and C. O. Kappe, Angew. Chem. Int. Ed., 2015, 54 (23), 6688-6728).
[3] Taming hazardous chemistry by continuous flow technology (M. Movsisyan, E. I. P. Delbeke, J. K. E. T. Berton, C. Battilocchio, S. V. Ley and C. V. Stevens, Chem. Soc. Rev., 2016,45, 4892-4928).
To learn more about the R-Series system, click here
To download a list of all 1100 publications citing Vapourtec, click here