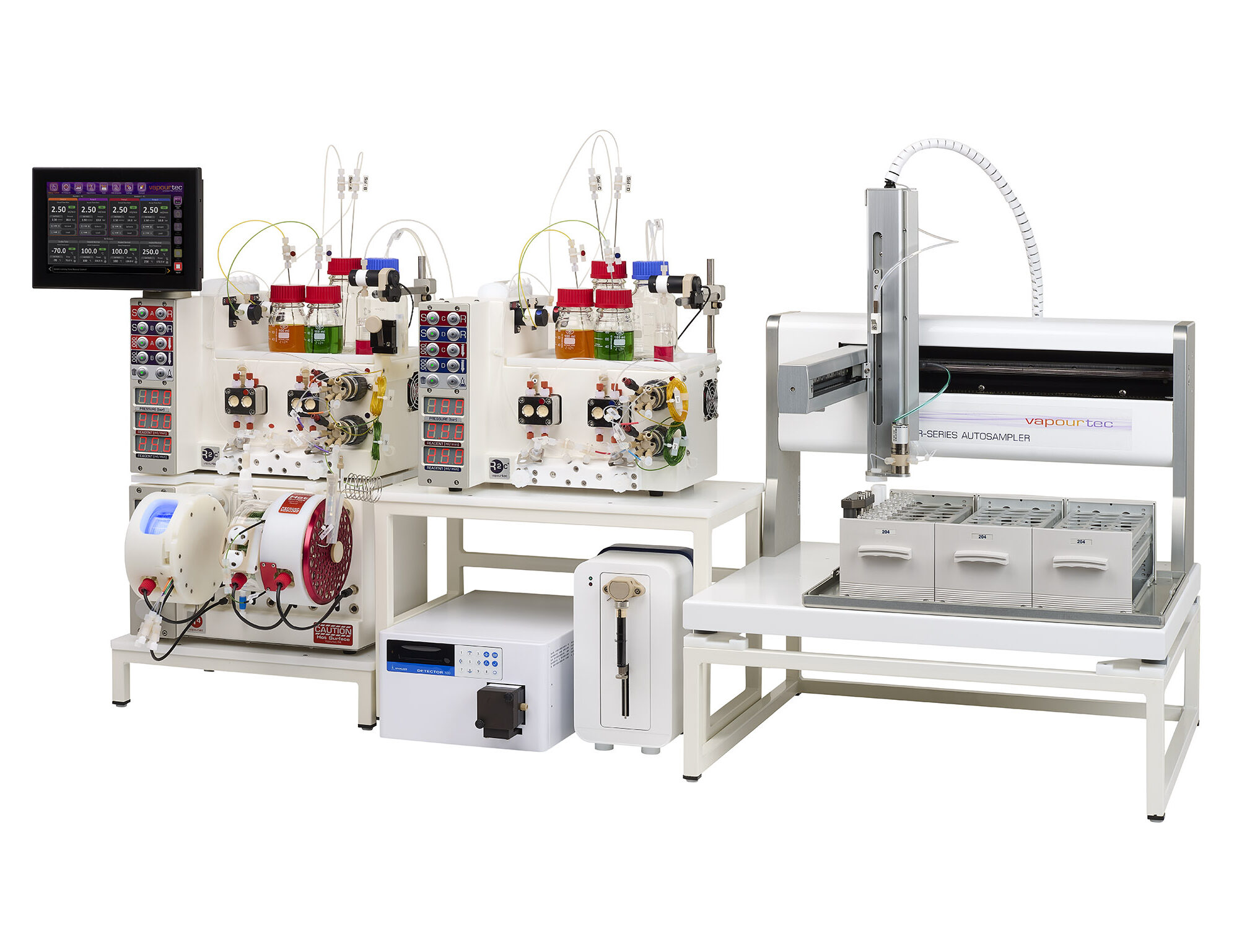
Date: 10 January 2025 | Category: News
Authors: Simone Marchetti, Cristopher Tinajero, Gianluca Palmara, Eduardo García-Verdugo, Ignazio Roppolo, Marcileia Zanatta, Victor Sans
Victor Sans, Marcieleia Zanatta and co-workers, from the Materials for Advanced Sustainable Production group at Jaume I University in Spain, have successfully used the Vapourtec R-Series flow chemistry system and an immobilised catalyst, formed through an epoxy-functionalized acrylate-based 3D printable ink, that allows the synthesis of cyclic carbonates through the selective cycloaddition of CO2 to epoxides [1]. Using traditional batch reactors for these transformations leads to issues with efficiency, cost and safety, while employment of continuous flow technologies allows access to lower reaction temperatures, shortened reaction times and enhanced scalability.
Figure 1: Schematic of the transformation of epichlorohydrin into a cyclic carbonate through selective cycloaddition of CO2.
3D printed resins allow bespoke reactor design
One of the key outcomes from this work was the use of 3D printing to generate a resin that was suitable for use as a microreactor; in engineering terms this requires a 0.6 mm gap between solid layers. Once the most suitable formulation was identified, the shape of the reactor was investigated. Previous work had shown that spiral structures were best for converting CO2 into cyclic carbonates [2], with adjustments to the helical pitch and installation of columns required to bolster strength and optimize flow conditions. Once the reactor was printed, functionalization of the polymeric surface was undertaken, giving a polymer bound ionic liquid within a bespoke 3D-printed reactor that was optimized for the reaction.
Victor Sans, Associate Professor in Chemical Engineering of Universitat Jaume I (Spain) commented “These are highly challenging solid-gas-liquid transformations, which can be carried out much more easily under continuous flow. The tailored design of the structured catalytic reactors enables much better contact between the reagents and the supported catalysts, allowing an intimate contact that enhances the kinetics of the reaction. Furthermore, the advanced geometric designs fabricated with additive manufacturing reduce or eliminate mass-transfer limitations and reduce pressure drop in the structured devices.
We are very interested in systematically designing and fabricating structured reactors with tailored geometries to develop sustainable chemical processes for various chemistries. The applications developed range from high-added value transformations for the pharma and fine industry, to the transformation of biobased feedstocks and CO2 capture and valorization for decarbonization of the energy and chemical industries. The effective digitalization of our R&D, including the employment of automated reaction platforms, 3D printing, and in-line analytics with tailored AI algorithms for the control, discovery, and optimization of the processes studied are the key enablers to achieving our goals”.
Vapourtec RS-400 pump allows plug-and-play of bespoke reactors
A continuous flow automated rig was used to evaluate the catalytic performance of the different geometries prepared. The 3D printed geometries loaded with ionic liquid catalyst were packed into a glass column and integrated into the reaction platform. A solution of epichlorohydrin in isopropyl alcohol was passed through the geometry with carbon dioxide gas introduced using a Vapourtec R-Series system, forming 4-(chloromethyl)-1,3-dioxolan-2-one. It was shown that:
- Catalytic activity was inversely dependent on the helicoidal pitch from the reactors
- A quasi-linear correlation was observed between the yield and the space time yield (STY) and the surface area of the printed reactor
- Higher resolution during the printing process was critical to enable more efficient performance of the structured reactors
Overall, a STY of 65 g L–1 h–1 was achieved, which is an order of magnitude improvement over previously reported values for 3D-printed ionic liquid reactors and fourfold that of a packed bed reactor. Finally, a long-duration experiment was undertaken over 72 hours, where there was no loss of catalytic activity.
The use of 3D printing enabled optimization of the reactor design and a degree of control over the functionalisation of the reactor surface. In addition, incorporation of a Vapourtec R-Series system allowed facile evaluation of catalytic performance, even when using gases, which can be challenging.
References:
[1] High-resolution 3D printable inks based on functional polymeric ionic liquids for applications in carbon dioxide valorization (S. Marchetti, C. Tinajero, G. Palmara, E. García-Verdugo, I. Roppolo, M. Zanatta and V. Sans, Additive Manufacturing, 2024, 89, 104304−104313). https://doi.org/10.1016/j.addma.2024.104304
[2] Multi-step oxidative carboxylation of olefins with carbon dioxide by combining electrochemical and 3D-printed flow reactors (D. Iglesias, C. Tinajero, S. Marchetti, I. Roppolo, M. Zanatta and V. Sans, Green Chem., 2023, 25, 9934–9940). https://doi.org/10.1039/D3GC03360K